High-voltage DC contactors (HVDC Contactors) play a vital role in modern power systems. To select the right contactor, you must understand its key parameters to ensure its reliability and efficiency in various application scenarios.
HVDC contactors depend on voltage, current, and insulation ratings for optimal performance in modern power systems.
Choosing the correct contactor affects performance, safety, and cost-efficiency. Let’s delve deeper into these parameters.
Why Are Voltage Ratings Crucial in HVDC Contactors?
Voltage ratings define a contactor’s capability to handle high-voltage DC circuits. It’s the first parameter to evaluate in any application.
The voltage rating determines the ability of the contactor to operate in a high-voltage DC circuit. This is the first parameter to evaluate when selecting any contactor. According to the parameter table in the picture, the maximum operating voltage of the HCF series contactor can reach 2000VDC, and its different derivative models support load voltages of 450V, 800V, 1000V, 1500V, and 2000V respectively.
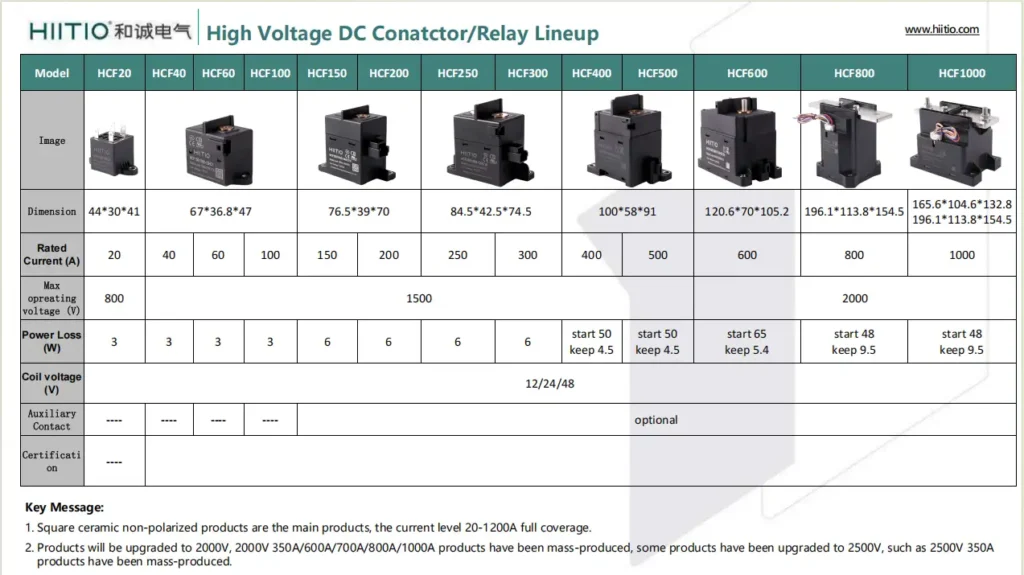
How Voltage Ratings Influence Performance
The voltage rating in the high-voltage DC system not only affects the safety of the contactor but also determines its reliability in actual use. For example, the HCF200A contactor:
- 450V model supports an electrical life of 1200 times (resistive load), suitable for industrial automation equipment or medium and low voltage applications.
- 1000V models are suitable for photovoltaic systems and other fields and can achieve 500 breaking operations (150A) and 6000 closing operations.
- 1500V and above models are specially designed for electric vehicle charging and HVDC transmission, can withstand higher voltages, and provide 10,000 breaking life under specific loads.
Voltage Rating (V) | Applications | Key Considerations |
---|---|---|
100–500 | Industrial automation equipment | Moderate insulation requirements |
500–1000 | Renewable energy systems | High insulation to prevent arcing |
Above 1000 | EV charging, HVDC transmission systems | Requires advanced insulation materials |
Optimization suggestions:
In photovoltaic systems, voltage surges during operation need to be prevented. It is recommended to use contactors with a rated voltage of at least 1000V to ensure long-term stable operation.
What Role Does Current-Carrying Capacity Play?
Current-carrying capacity reflects the performance of the contactor under continuous load current.
For example, the rated current of the HCF series contactor is 200A, and the short-term current-carrying capacity can reach the following levels:
- 250A: 15 minutes
- 320A: 5 minutes
- 600A: 30 seconds
- 2000A: 0.6 seconds
Overload Capacity Analysis
Under high voltage environments, the contactor also needs to have good overload disconnection capacity. Taking the 450V model as an example, its maximum disconnection current is 2000A, which is crucial in energy storage systems or DC fast charging piles to ensure the safety of equipment in extreme conditions.
Optimization suggestion:
For scenarios that require long-term high current carrying, such as electric vehicle charging stations, it is particularly important to select contactors with strong overload capacity and high short-term current-carrying capacity.
How Does Contact Resistance Affect Performance?
Contact resistance directly affects energy loss and heat generation.
For example, the contact voltage drop of the HCF series contactor at a rated current of 200A does not exceed 0.1V, and the corresponding contact resistance is less than 0.5mΩ, which ensures efficient current conduction and reduces energy consumption.
Heat and Life Relationship
Excessive contact resistance will cause heat accumulation and accelerate the aging of contactor components.
Dive Deeper: Why It Matters
High contact resistance leads to heat buildup, which can degrade contactor components. Manufacturers often provide this value in milliohms. Look for contactors with resistance under 0.5mΩ for high-efficiency systems.
Contact Resistance (mΩ) | Energy Efficiency | Maintenance Frequency |
---|---|---|
< 0.5 | Excellent | Rarely required |
0.5–3.0 | Moderate | Moderate intervals |
> 3.0 | Poor | Frequent inspections needed |
Optimization suggestion:
In high-efficiency systems (such as photovoltaic inverters and energy storage systems), models with lower contact resistance are preferred to reduce heat loss in long-term use.
Why Is Insulation Strength a Key Parameter?
Insulation strength is an important indicator for contactors to avoid arcing or breakdown under extreme voltages. HCF series contactors have the following insulation performance between the main contacts and the coil:
- Dielectric withstand voltage: ≥4000VAC before test, ≥2500VAC after test (1 minute)
- Insulation resistance: before test ≥1000MΩ (1000VDC), after test ≥50MΩ (1000VDC)
Insulation Design and Materials
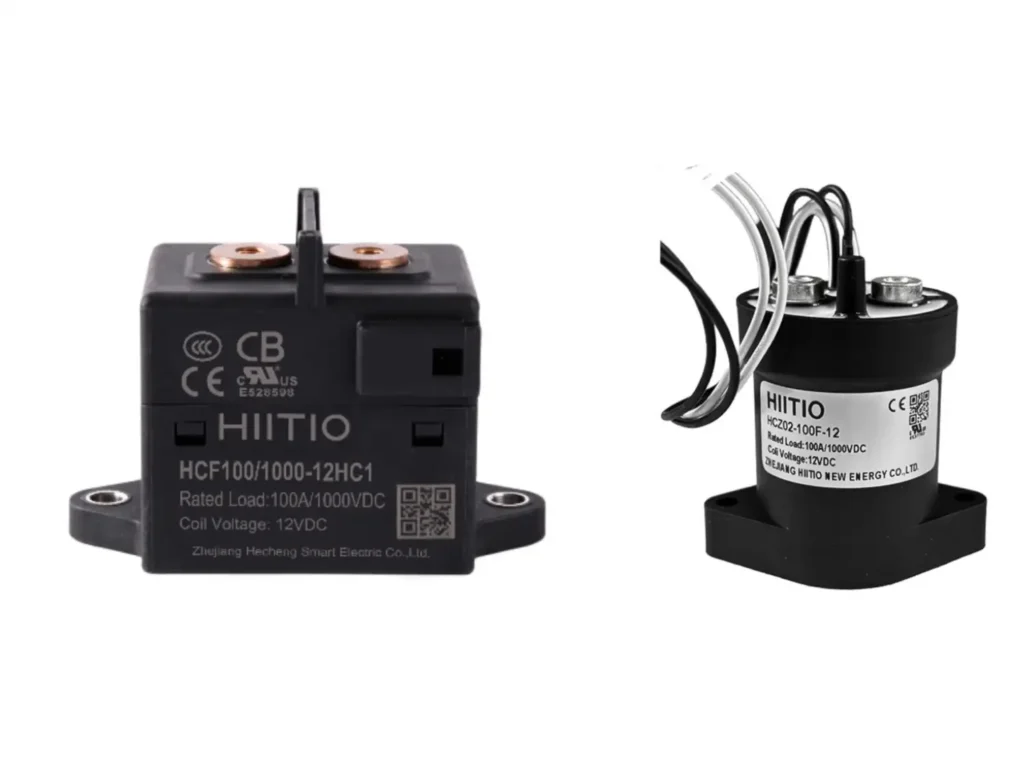
Insulation is often made from specialized exploys or ceramics. These materials ensure reliability under stress, especially in fluctuating environments like renewable energy grids.
Insulation Material | Advantages | Applications |
---|---|---|
Exploy | Flexible and cost-effective | EV charging |
Ceramic | Heat-resistant and durable | Industrial automation |
Mechanical Properties and Environmental Adaptability
HVDC contactors need to operate in harsh environments, so mechanical properties and environmental adaptability are also crucial. HCF series contactors have the following characteristics:
- Vibration resistance: 5.79G (random vibration, 10-2000Hz)
- Impact resistance:
- Functionality: 20G, half-sine wave 11ms
- Destructiveness: 50G, half-sine wave 6ms
- Pull-in time: maximum 30ms
- Release time: maximum 10ms
Mechanical Life
The mechanical life can reach 200,000 times, which is suitable for scenes requiring frequent operation.
Optimization suggestion:
For applications requiring higher mechanical life, such as industrial automation or energy storage equipment, choose models with stronger vibration resistance and longer life.
Optimization of Coil Parameters
The coil parameters directly affect the response speed and energy consumption of the contactor.
For example, the coil voltage range supported by the HCF 200A series contactor is:
- 12VDC, 24VDC, 48VDC
- Pull-in voltage: < 75% rated voltage (such as less than 9V for 12V coil)
- Release voltage: > 10% rated voltage (such as greater than 1.2V for 12V coil)
The coil power consumption is about 6W, and the maximum allowable voltage is 1.33 times the rated voltage (such as the maximum voltage of 12V coil is 16V).
Optimization suggestion:
In low-power systems, choose coil versions with lower power consumption and shorter response time to achieve energy savings.
Application Scenario Recommendations
Combined with the above parameter analysis, the following are recommended application scenarios and applicable models:
- Photovoltaic system: models above 1000V, with excellent insulation performance and contact resistance performance.
- Electric vehicle charging pile: 1500V model, rated current 200A, excellent overload protection capability.
- Energy storage system: 450V model, long mechanical life, and short pull-in time.
Conclusion
By deeply analyzing these core parameters, we can select the optimal contactor model according to specific needs to achieve efficient, safe, and long-term stable operation of the system. High-voltage DC contactors are the backbone of modern power systems. Key parameters like voltage ratings, current capacity, contact resistance, and insulation strength define their performance. Evaluating these metrics ensures reliability and safety across diverse applications.